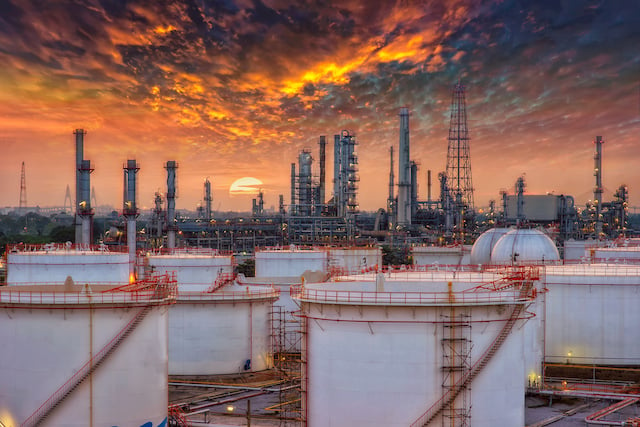
The INCOLOY range of nickel alloys are commonly used within a number of different industries. INCOLOY alloy 800 was the first in the 800 series of alloys, invented in the 1940s. The series is built around nickel, iron and chromium, meaning they retain many of the corrosion and high-temperature resistant properties of the advanced INCONEL range, but are more economical being less nickel-heavy.
They are certainly not inferior alloys, however, and they have a solid reputation for their high strength and exceptional resistance in some of the most extreme processing environments.
One popular INCOLOY product is INCOLOY alloy 803. This material was developed to be used in very high-temperature environments, with a carefully balanced chemical composition to enhance its corrosion resistance. In particular, it can withstand high-temperature corrosion, including oxidation, carburisation and sulfidation. This type of heat-resistant alloy is often used in applications within a mixed oxidant carburising environment. Carburization can cause a loss of an alloy’s creep and stress-rupture strength, and a reduction to thermal fatigue. Which is why highly resistant alloys like INCOLOY alloy 803 are so useful, as they are less likely to fail in service operation.
Chemical and mechanical properties
The secret to the alloy’s success lies in its chemical composition. It has consistent values of 32-37% nickel and 25-29% chromium in its makeup – higher than in both the INCOLOY alloy 800H and 800HT Grades. This is what lends the material its excellent resistance to the high-temperature corrosive media, as well as good long-term thermal stability.
Additionally, the alloy has controlled amounts of manganese, aluminium and titanium, with the balance being made up of iron. The ratio of the key elements have been engineered to provide the optimum properties at very high temperatures, from 840°C (1550°F) to 1150°C (2100°F). As such, it is used widely in petrochemical processing, as well as chemical and thermal processing. Due to its ability to resist stress-rupture and good fabrication capabilities, it has been used in the newest generation of reformer furnaces.
INCOLOY alloy 803 also has a good range of mechanical properties. For example, it exhibits good mechanical strength at both room and elevated temperatures. Even in high-temperature conditions, its tensile and impact strength remains good, proving its thermal stability. But, as with all similar iron-nickel-chromium alloys used for high-temperature service, it can undergo solid-state reactions when exposed to intermediate temperatures between 590°C (1110°F) and 815°C (1500°F) for a significant amount of time. This reaction can result in a reduction in the ductility and impact strength of components. As with any alloy, design engineers must weigh these factors against the service conditions for alloy components.
Applications for INCOLOY alloy 803
Because of its unique properties and cost effectiveness, one of the key areas where INCOLOY alloy 803 is employed is within the petrochemical process industry. These complex environments are high temperature, corrosive and volatile.
Materials used within petrochemical-processing systems must be able to withstand the synthesis in Fischer-Tropsch reactors and associated equipment. The Fischer-Tropsch process converts a mixture carbon monoxide and hydrogen into liquid hydrocarbons. It’s an important reaction in both coal liquefaction and gas-to-liquids technology.
In order to meet the high specifications within this industry, design engineers often turn to the INCOLOY range of alloys. The series is often utilised in coal, gas and biomass collection, storage and conversion systems.
INCOLOY alloy 803 is one of the most commonly used materials for those looking for a technically superior material that can withstand these intense conditions. It’s particularly useful for its aforementioned exceptional corrosion resistance against oxidation, sulfidation, carburisation and nitridation at elevated temperatures.
The alloy exhibits good stress-rupture strength and high resistance to carburisation and cyclic oxidation, as well as preventing thermal distortion and embrittlement. Due to these distinct properties, INCOLOY alloy 803 is used widely across the petrochemicals industry, particularly for ID-finned pyrolysis tubing in high-severity ethylene furnaces.
INCOLOY alloy 803 is also used within the chemical and thermal processing industries, and oil and gas pipelines. Within oil and gas, applications can include flow lines in subsea walls, tubing and processing liquefied natural gas.
Versatile product range
INCOLOY alloy 803 is easily fabricated and welded, which makes it very versatile. It can be formed by both hot or cold working, though forming at temperatures of between 650°C and 870°C (1200°F and 1600°F) can result in cracking.
It also has good welding characteristics, especially in the forming of harps with associated weldolets. The alloy has the same weldability as INCOLOY alloy 800H. It should be joined using materials that have similar high-temperature strength and corrosion resistance to retain the alloy’s properties. In most cases, welding with INCONEL Welding Electrode 117 and INCONEL Filler Metal 617 will suffice. However, for sulfidation environments, the recommended welding products are INCONEL Welding Electrode 152 and INCONEL Filler Metal 52.
The alloy is available in all major product forms with different finishes and tempers, meaning it can be manufactured to suit the needs of any project. It can even be produced as internally finned – either straight or spiralled fins – cold-finished tubing.
Thinking about using INCOLOY alloy 803 in your next project? Give us a call today and discuss your requirements to see if it’s the right material for you. Contact our experienced sales team today.