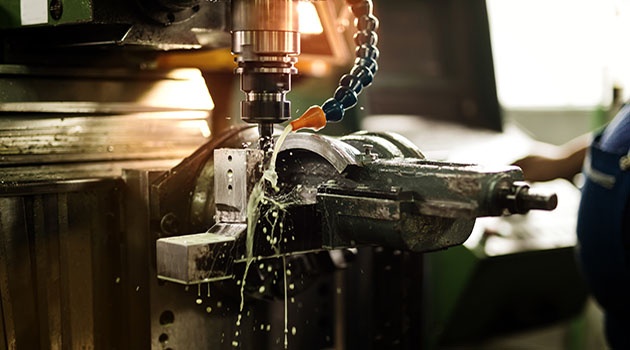
Iron is, by mass, the most common metal on Earth. Pure iron is quite soft, but it is hardened and strengthened by other elements, most often carbon to form steel and other iron alloys. Steel is one of the most used materials of construction around the world for industrial uses, thanks to its combination of low cost and high strength.
But iron is also a component in many of the technically superior nickel-chromium alloys that Corrotherm supplies. The role it plays within these alloys varies, with its inclusion kept within strict compositional limits to create high-quality alloys with desirable qualities.
For example, in materials like INCONEL alloy 625, iron is limited to a maximum of just 5% in order to retain the outstanding corrosion resistance that the alloy is known for. Nickel-chromium-iron alloys do play an important part in many industries. INCONEL alloy 600, which has 6-10% iron present, is a standard material in the chemical industry, as well as for automotive engines, aerospace engines and airframes. This is achieved by carefully applying chemical composition limits and processing precisely to avoid pitting and the risk of stress corrosion cracking.
Alloys with a higher iron content
Iron is used more prominently in some of the INCOLOY series of alloys. These alloys are leaner nickel versions of the INCONEL range, which offer more economical solutions that can be used in corrosive and high-temperature environments. The lower quantities of nickel are made up for using higher amounts of iron.
INCOLOY alloys 800H and 800HT both have the same base metals, with nickel, chromium and iron in controlled balance. The iron content is a minimum of 39.5% in each of the alloys. The alloys are known for their high strength in extreme temperatures, as well as resistance to oxidation, carburization and other types of high-temperature corrosion. The materials were first created in the 1950s to meet the demand for heat- and corrosion-resistant alloys with a lower nickel content.
Iron plays an important role in these alloys. In some service environments with atmospheres that are oxidising to chromium but reducing to nickel, the nickel-chromium alloys could be subject to internal oxidation, which can cause severe embrittlement. The addition of iron can help to decrease this risk, and the high quantity of iron in INCOLOY alloy 800H and INCOLOY alloy 800HT means that both metals are resistant to internal oxidation.
Other alloys with a significant iron content include INCOLOY alloy 825 and INCOLOY alloy 925.
Restricting iron
Some alloys have strict limits on the iron content to maintain their properties. For example, INCONEL alloy 22 is a fully austenitic advanced corrosion-resistant alloy mainly consisting of nickel, chromium, molybdenum and tungsten. Its iron content is maintained at between 2% and 6%, but typically at less than 3%.
As it is used in chemical and petrochemical processing, its ability to resist aggressive media is key to its use. In an acid chlorine environment, its combination of high molybdenum and tungsten content, balanced with the low iron content, helps to provide superior pitting resistance.
Find out more about the compositional makeup of every one of the alloys that Corrotherm supplies via the Grades page. To discuss your requirements, please Contact Us.