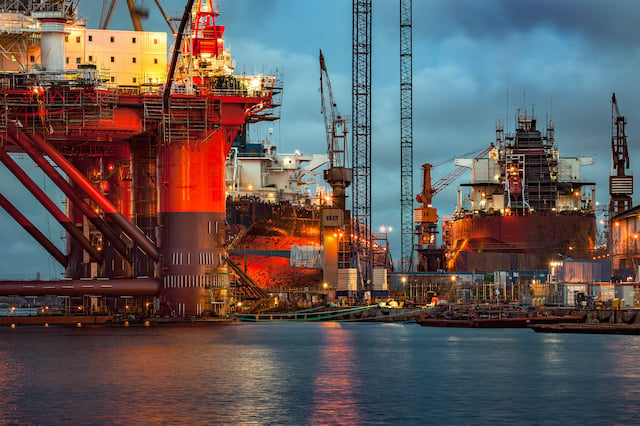
Our need for reliable energy continues to grow around the world, so it’s essential to find ways to tap into natural reserves. Subsea operations are vital, whether that’s to access oil and gas fields located offshore, or the installation of offshore wind power structures. However, fully submerged oceanic structures produce many technical problems for design engineers, especially when it comes to material selection.
Subsea environments in the oil and gas industry are particularly difficult. The presence of seawater puts materials and equipment under immense pressure, and leaves them open to corrosive attack from outside elements. Equally, they are subject to corrosion from the inside too. Structures are used for the exploration, drilling and development of oil and gas fields in UK waters and offshore.
High-performance nickel alloys are perfect for use in a subsea environment. They are highly resistant to corrosion by seawater, which is why they are often selected for use in these projects. Nickel alloy properties also include the ability to withstand high pressure and they are exceptionally strong. They have been designed specifically to be used in some of the most extreme environments in engineering.
INCONEL alloys in subsea projects
The flagship nickel alloy of the INCONEL range, INCONEL alloy 625, is an excellent choice for seawater applications. Its unique combination of nickel and chromium, balanced with measured amounts of molybdenum, iron and niobium, gives the metal industry-leading corrosion resistance. It offers resistance against pitting and crevice corrosion, which are common in marine use. It also offers high corrosion-fatigue strength, high tensile strength and resistance against chloride-ion stress-corrosion cracking. As such, it is used for a wide range of subsea applications, including components for submerged controls and fittings.
INCONEL alloy 22 is also useful for some subsea situations. This fully austenitic nickel alloy has a high level of chromium with significant additions of molybdenum, titanium and tungsten. It is particularly resistance to aqueous corrosion, as well as wet corrosion by both oxidising and reducing media. It’s also exceptionally resistant to attack by both stagnant and flowing seawater.
Another material that has been specifically designed for severely corrosive environments in INCONEL alloy 725. It is broadly similar to INCONEL alloy 625, however it is age-hardened to offer twice the strength of its predecesor. It is optimal for use in situations that require a higher level of strength without compromising on corrosion resistance. As it is highly resistant to pitting and crevice attack by seawater, it is often used for fasteners in marine applications. Data shows that INCONEL alloy 725 is superior to INCONEL alloy 625 when it comes to crevice corrosion initiation in seawater.
While better known for its exceptional performance in chemical processing, INCONEL alloy C-276 is no stranger to aggressive environments, and seawater is no exception. It exhibits excellent resistance to seawater corrosion, especially crevice conditions that might attack other commonly used subsea materials, such as INCONEL alloy 625 and MONEL alloy 400 (see below).
Furthermore in the INCONEL range of alloys, both INCONEL alloy 690 and INCONEL alloy 693 are used for various subsea applications. INCONEL alloy 690 is a high-chromium nickel alloy, which shows great resistance to aqueous conditions. It also operates in high-temperature conditions. Meanwhile, INCONEL alloy 693 evolves INCONEL alloy 690 further, retaining the benefits of the high chromium content, but with the addition of approximately 3% aluminium to give added resistance to high-temperature corrosion in numerous severely corrosive environments.
Applications of the INCOLOY range
The INCOLOY range of nickel alloys should not be overlooked for subsea operations either. These leaner-nickel versions of the INCONEL range can be more economical, while still being more than fit for purpose in a way range of applications.
For example, INCOLOY alloy 825 is a popular choice for oil well and gas gathering pipes, both natural and sour gas. It is highly resistance to general, crevice and intergranular corrosion, as well as stress-corrosion cracking in seawater-based environments.
INCOLOY alloy 925 offers a perfect blend of molybdenum, copper, titanium and aluminium, alongside significant nickel, iron and chromium elements. This potent mix results in an alloy that is both incredibly strong and highly resistant to many types of corrosion. Its applications include down-hole gas-well components, marine shafts and high-strength piping systems for both natural and sour gas environments. It’s also used for marine fasteners, where its high strength is a real bonus.
Finally, INCONEL alloy 800 is a classic material. That has been around for a long time now – it was introduced to the market in the 1950s. While it has been superseded in some ways by more advanced, modern materials this is still a versatile all-rounder in some subsea applications. It offers good general corrosion resistance to aqueous environments, including high temperatures.
When MONEL is used
MONEL alloy 400 is also employed within subsea environments. This nickel-copper alloy is strong and versatile. It has a good level of corrosion resistance in many situations, which includes rapidly flowing seawater. This makes it useful for a wide range of marine applications.
It is also resistant to both biofouling and MIC (Microbially Influenced Corrosion), two major problems associated with subsea operations. As such, MONEL alloy 400 can be used for the manufacture of wave protection sheathing for platform risers and steely pylon legs on offshore rigs.
Corrotherm is a nickel alloy stockist and supplier. To find out more about the Grades we offer for subsea environments, Contact Us today.