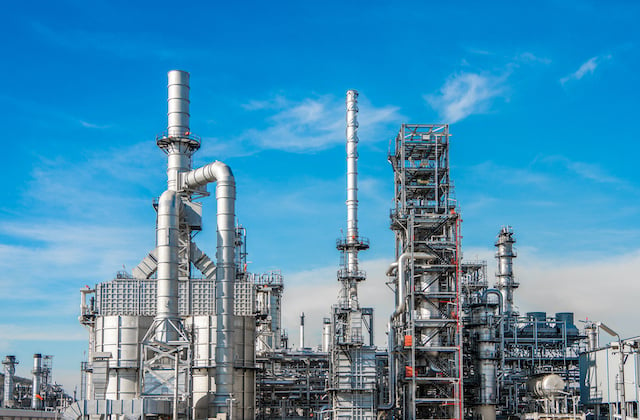
INCONEL alloy 617 is a true sum of its parts. It is a blend of nickel, chromium, cobalt, and molybdenum, with each component element adding to its impressive specifications.
The high levels of both nickel (44.5% minimum) and chromium (20-24%) give the alloy a good resistance to both reducing and oxidising media. Cobalt (10-15%) and molybdenum (8-10%) combine to impart solid-solution strengthening. A small quantity of aluminium (0.8-1.5%) is also included, to work alongside the chromium to give good oxidation resistance at high temperatures.
One of this alloy’s key characteristics is that it can retain a high strength level, even at elevated temperatures, without compromising its corrosion resistance. The material is also very practical, as it can be readily formed and welded using conventional techniques.
With all of these benefits, it’s no wonder that INCONEL alloy 617 is widely used across a range of industries, where high-temperature corrosion resistance and strength is required.
Corrosion resistance
INCONEL alloy 617 is resistant to a wide range of corrosive media, which is what makes it so versatile. It exhibits a high level of corrosion resistance against oxidation and carburisation. It is of particular use in wet corrosive environments.
Under tests, the material has the ability to form and retain an oxide layer, which acts as a protective shield against corrosion. Even when exposed to extreme temperatures of 1150°C (2100°F), is proves highly resistant to oxidation. This is thanks to its inclusion of chromium and aluminium, which are responsible for the formation of the oxide particles on the surface. The fact that this layer forms so rapidly as the temperature increases means the alloy isn’t vulnerable to attack.
The alloy also has excellent resistance to carburisation as well as oxidation. Tests show that in gaseous carburising environments at an elevated temperature, INCONEL alloy 617 outperforms other carburisation-resistant alloys, including INCONEL alloy 600 and INCOLOY alloy 800.
The alloy also has excellent resistant to aqueous corrosion, though its main applications tend to be volatile, high-temperature environments.
Mechanical properties
As well as its excellent corrosion resistance over a large range of temperatures, INCONEL alloy 617 also has good mechanical properties. It maintains a high level of strength, even at elevated temperatures. Its corrosion resistance contributes to the material’s consistent strength values, making it a very useful and versatile alloy.
It can be fabricated through standard forming, machining and welding procedures. One thing to bear in mind is that, although it has good formability, it does require high forces due to its inherent strength under elevated temperatures. It has broadly the same hot-forming characteristics as INCONEL alloy 625. It can also be cold formed, but its work-hardening rate is high.
Usually, to make the most of its strength properties, INCONEL alloy 617 is used in solution-annealed condition. This provides a coarse grain for the best creep-rupture strength and bend ductility. Solution-annealed INCONEL alloy 617 also has good metallurgical stability, which is due to the formation of carbides and the precipitation of gamma prime phase at elevated temperatures. The high creep-rupture strength that can be achieved, even at temperatures of 980°C (1800°F) and above, make this alloy suitable for long-term, high-stress use.
The alloy can be welded with ease too. INCONEL Filler Metal 617 is used for gas-tungsten-arc and gas-metal-arc welding; INCONEL Welding Electrode 117 is used for shielded metal-arc welding. By using these filler metals, which match the composition of the base metal, the strength and corrosion resistance of the alloy is retained.
Applications
INCONEL alloy 617 is considered an attractive material for many components, such as combustion cans, and transition liners in both aircraft and land-based gas turbines. Its excellent resistance to high-temperature forms of corrosion, also means that it is used for catalyst-grid supports in the production of nitric acid, for heat-treating baskets, and for reduction boats in the refining of molybdenum.
It also finds its use in power generation (for both fossil and nuclear fuel). It’s being used more often for reformer tubes in steam generation at petrochemical plants, as well as high-temperature gas components.
These advanced alloys are important in helping engineers and designers to produce new products. INCONEL alloy 617 is a good candidate for the latest generation of ultra-supercritical boiler tubes. The alloy has been incorporated into the ASME Boiler and Pressure Vessel Code for nuclear applications at high temperatures; this code regulates the design and construction of boilers and pressure vessels. One application is in molten salt reactors (MSR), a type of nuclear fission reactor – its predecessor, INCONEL alloy 600, was used in an aircraft reactor experiment (early MSR research) back in 1954.
Similar alloys
INCONEL alloy 617 builds on the success of its predecessor, INCONEL alloy 601, which also offers high nickel and chromium levels, plus aluminium to give excellent resistance to high-temperature oxidising atmospheres. It is still widely employed as thermowell sheathing material and in oxygen injection tubes in the metal- and glass-making industries, alongside other key uses.
If an even more advanced alloy in required, it’s also worth considering INCONEL alloy 625, which is one of the most versatile alloys available, offering high strength, excellent fabricability and outstanding corrosion resistance. It offers a similar base composition of elements to INCONEL alloy 617, with high quantities of both nickel and chromium, as well as molybdenum. However, it also has niobium, which helps to provide particularly high strength in an annealed condition without a deliberate strengthening heat treatment.
To find out more about all of the available INCONEL alloys, visit our Grades section. To discuss your requirements with a member of our Sales team, then please Contact Us.