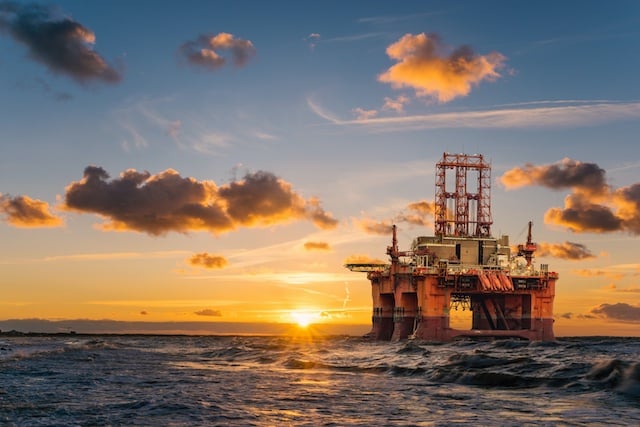
The MONEL series of alloys has been in existence for more than 100 years. It was first created back in 1901 by Robert Crooks Stanley, a man sometimes considered the ‘Grandfather of the nickel industry’. It was developed while he worked for the International Nickel Company (INCO), and patented in 1906.
This valuable Grade is primarily composed of nickel and copper, and is a good alternative to commercially pure nickel, offering similar corrosion-resistant properties in a more cost-effective manner. The nickel and copper blend is mixed with carefully controlled amounts of other elements, including iron, manganese, silicon, carbon and sulphur, which together give the MONEL range of alloys its distinctive properties.
One of the advantages that the alloy has over commercially pure nickel is that is stronger and it is readily fabricated for a number of end uses. It is a single-phase alloy, given that both nickel and copper are mutually soluble in all proportions, which can be used in environments that are highly corrosion or at either extreme of the temperature scale.
MONEL alloy 400
MONEL alloy 400 was created as a binary alloy with the same proportions of nickel and copper as found naturally occurring in meteoric nickel ore. This means that it is considered a ‘puritan alloy’, or something that is found in its pure form in nature.
MONEL alloy 400 is the basis of the MONEL range, with specialist versions having been created in the years since its inception. For example, MONEL alloy 401 is designed for use in electric and electronic applications. MONEL alloy 404 is often used for transistors and other such delicate components that benefit from the very carefully balanced and controlled version of this technical alloy. MONEL alloy 405 is a free-machining grade of the original alloy, with only the sulphur element increased to meet very specific needs – usually automatic screw machine stock. MONEL alloy 450 is adapted for use in seawater applications and saltwater piping, among other uses. Each version of the original MONEL product has similar desirable mechanical and chemical properties.
MONEL alloy 400’s excellent mechanical properties means that it is often deployed in sub-zero temperatures, where its strength and hardness increase with only minimal impact on its ductility. Many other materials in these conditions would encounter a ductile-to-brittle transition in such low temperatures. In terms of shear strength, a previous US Navy tear test took the material down to temperatures of -320°F where it retained its excellent ductility, with its maximum load increasing considerably with the lowering temperatures.
It is also a material that is known for its exceptional toughness and impact strength, which it retains over a wide range of temperatures. It can be used in high-temperature applications up to 1,000°F in oxidising conditions, and even higher if in reducing conditions.
It’s no real surprise, then, that MONEL alloys are used in the aerospace industry, where strength and resistance are primary factors in material selection. During the 1960s it was widely used in the construction of aircraft, including experimental projects such as the North American X-15. It is still used in aerospace today for critical wiring in high-temperature conditions, though stainless steel wire is also used in other areas to save costs.
For the last 100 years, it has been employed in the oil and gas industry, mainly in petroleum tower internals, fasteners and fittings, and pumps. Another important use is as sheathing protection for offshore structures in the splash zone and sub-sea. It’s been found to offer good corrosion protection, as well as resistance to physical damage.
MONEL alloy K-500
While MONEL alloy 400’s mechanical properties are already impressive enough, one of the most-used versions of the Grade is the precipitation-strengthened MONEL alloy K-500. The significant difference is that the composition includes small, controlled amounts of both titanium and aluminium. These are added during melting to the basic MONEL alloy 400 mix, with the intention of making a material with even greater strength and hardness without compromising the excellent corrosion-resistant properties.
As the MONEL mixture is heated and the additional elements added, sub-microscopic particles of the titanium and aluminium are precipitated throughout the alloy’s matrix. This age-hardening gives way to a MONEL alloy that is commonly used for pump shafts, doctor blades, oil well drill collars and electronic components, where the extra hardness is required.
MONEL alloy K-500 is outstanding in tests to measure its mechanical performance, with tensile and yield strengths increasing with decreases in temperature, with very little effect on the ductility or toughness. It avoids the ductile-to-brittle transformation, even in cryogenic conditions. Tests on its shear strength, impact strength and fatigue strength have also been extensively performed, with results showing that it offers an exceptional level of strength across the board – the full results of which can be viewed in the material’s data sheet.
MONEL by comparison
In comparison to MONEL alloy 400(ref.), MONEL alloy K-500 offers superior fatigue strength (230-290 MPa vs 260-560 MPa), shear strength (370-490 MPa vs 430-700 MPa) and tensile strength (ultimate UTS; 540-780 MPa vs 310-880 MPa).
However, material selection between MONEL alloy 400 and MONEL alloy K-500 very much comes down to the end application. While K-500 has increased mechanical toughness and hardness, it is more susceptible to stress-corrosion cracking in certain environments.
The two’s thermal properties are broadly similar, though MONEL alloy 400 has a higher Curie Temperature (40°C vs -67°C), which is the temperature above which materials lose their permanent magnetic properties. They are also pretty much identical when it comes to their electrical properties.
In many cases and applications, MONEL alloy 400 and alloy K-500 are used in combination, playing to each of their own strengths in the right areas within a project.
Find out more about the MONEL alloys that Corrotherm stocks on our dedicated pages, or Contact Us today to speak to an experienced member of our Sales team.