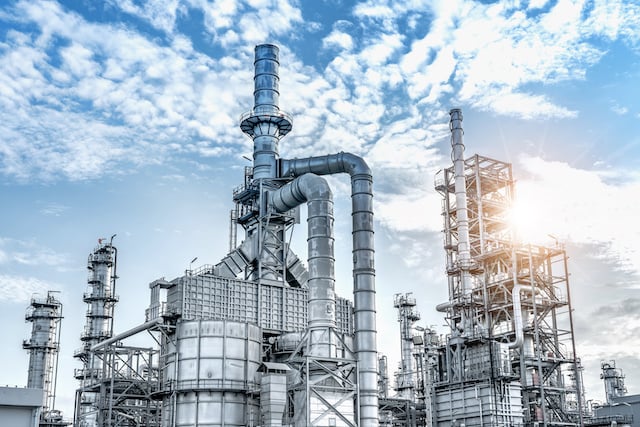
An incredibly versatile and useful material, INCOLOY alloy 825 is routinely used across the chemicals industry.
When it comes to handling and processing chemicals, there are many challenges. Chemicals, by their very nature, can be highly corrosive and the processes required to store and handle them often produce a lot of heat.
It’s important that the materials selected for any part of the industrial process are up to the task. Luckily, the latest developments in alloy production have created materials that are more than a match for even the most volatile of chemical processes.
Nickel alloys across the board have key properties that make them perfect for this industry. They are highly corrosion resistant and can cope with the high temperatures and pressures involved. These superior nickel alloys are used to create heat exchangers, furnaces, piping, pumps and valves.
Why INCOLOY alloy 825?
Of all the nickel alloys that Corrotherm supplies, INCOLOY alloy 825 is one that is well-suited to use in the chemicals industry. This material was one of the first to add molybdenum to its nickel-chromium-iron composition, and many other nickel alloys have built on its success since.
Despite being a forerunner to more modern nickel alloys, INCOLOY alloy 825 is still very much in use in the chemicals industry. As well as molybdenum, it includes both copper and titanium. Balanced with the high nickel (38-46%), iron (22% minimum) and chromium (19.5-23.5%) content, these elements all combine to create a material that is exceptionally resistant to many corrosive environments.
The material has earned its place in the chemicals industry thanks to the wide corrosion resistance it offers. It can resist chloride-ion stress-corrosion cracking, for example, it can withstand reducing conditions in the presence of sulfuric and phosphoric acids. The advantage of the molybdenum is that it gives the material resistance against pitting and crevice corrosion; while the chromium offers protection from oxidising substances like nitric acid, nitrates and oxidising salt. Titanium stabilises the material against sensitisation to intergranular corrosion, when correctly heat treated.
Uses and applications
As you can see, INCOLOY alloy 825 has been carefully produced to give it a range of properties that make it useful in the chemicals industry. It’s also used in pollution control, oil and gas recovery, acid production, pickling operations, nuclear fuel reprocessing and handling radioactive waste.
It’s not just its corrosion resistance that makes this nickel alloy so usable. It also exhibits good mechanical properties from cryogenic to moderately high temperatures, though it does have its limitations – see the full Data Sheet to find out more.
It’s also an easy material to work with, as it’s reasonably ductile. It can be worked quite readily and in a similar fashion to austenitic stainless steel. It needs to be carefully annealed, as the temperatures and processes used are imperative to the material’s high corrosion resistance.
If you would like to chat to us about your next project and find out more about INCOLOY alloy 825 and its properties, please get in touch.