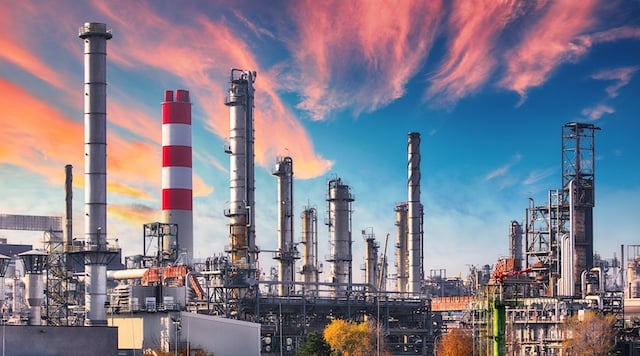
It’s not often that a high-performance alloy stays in such prominent use across multiple industrial applications for many decades, without being superseded by newer materials. However, INCONEL 625 bucks this trend and remains a standard construction material that experts continue to use time and again.
INCONEL 625 was developed in the early 1960s and became popular thanks to its versatility, enabling it to be used for multiple applications. Over more than half a century later, it continues to be well regarded as engineers find new ways to employ this indispensable alloy. Today’s uses for the nickel alloy go far beyond its original purpose in ultra-critical steam piping.
Throughout its lifetime, new processing methods have been introduced that have enabled engineers to better understand the capabilities of this alloy. For example, slight changes to its composition, as well as improved milling practice, have increased the fatigue life of thin sheet. It is also an excellent choice for welding and can accommodate dilution from other compositions, making 625 filler metals especially suitable for dissimilar welding.
Perfect composition
INCONEL alloy 625’s unique composition grants it desirable properties. It is a high-nickel alloy, with a minimum of 58% of the total blend. It also has a very substantial level of chromium (20-23%). The perfect mix of nickel and chromium imparts an extraordinary level of corrosion resistance, particularly to oxidising chemicals.
The inclusion of molybdenum (8-10%) gives the alloy its incredible high strength, as well as working with the nickel content to provide resistance in non-oxidising environments. The molybdenum is also the reason why this alloy is resistant to pitting and crevice corrosion.
While niobium is a smaller percentage of the composition, it is there to stabilise the alloy against sensitisation during welding, which prevents subsequent intergranular cracking. Together, every element in this high-performance alloy helps to create a material that is strong, resistant and highly workable, solving many of today’s design-engineering problems.
Key properties
There are a number of reasons why this alloy is so popular. In particular, its composition enables it to withstand a range of corrosive environments. In milder conditions, for example in the presence of freshwater or seawater, neutral salts and alkaline media, it is almost corrosion free.
In more aggressive low-temperature corrosive environments, the chromium in its makeup provides superior resistance against oxidising chemicals, and the molybdenum offers resistance to non-oxidising environments. It is also capable of withstanding hostile high-temperature environments.
The nickel alloy is also very strong. Its high strength is born from the combination of molybdenum and that little bit of niobium. Together these elements distort the alloy’s atomic matrix, which imparts particularly high strength in annealed condition without the need to strengthen deliberately via heat treatment. As such, the alloy is usually supplied in annealed condition to give the best stability during both fabrication and in use. Its strength comes in the form of high corrosion-fatigue strength, high tensile strength and resistance to chloride-ion stress-corrosion cracking.
Use in fuel refining
One of its key applications has been in fuel refining, where excessive corrosion can be a huge problem throughout the process. INCONEL 625 seamless pipe can help by inhibiting naphthenic acid corrosion, reducing polythionic acid (PTA) or chloride stress-corrosion cracking, and enhancing resistance to oxidising. It also reduces high-temperature sulphidation.
Naphthenic acid corrosion is an issue faced by refineries’ distillation towers operating at high-temperature environments of 220-400°C, especially in transfer lines, nozzles and return bends. INCONEL alloy 625 has been proven to provide good, long-term resistance to this type of corrosion in the industry and is typically used for distillation tower fabrication. It can also be used in overhead condensers at fuel refineries where material selection is dependent on a number of different factors, including the source of cooling water, the amount of chloride, PH control, water velocity and so on.
In hydrotreating units, where hydrogen is used to remove sulphur and nitrogen from different fuel and oil sources, materials need to be resistant to the effects of hydrogen sulphide (high-temperature corrosion), and ammonia and ammonium sulphide (lower-temperature corrosion and erosion-corrosion).
Similarly, hydrocracking units, which combine desulphurisation with cracking, can suffer from similar corrosion problems. While there are other alloys that can be used and offer good resistance to the hydrogen sulphide in normal operating temperatures, they don’t all offer the additional benefits of reducing PTA stress corrosion cracking and intergranular attack that INCONEL alloy 625 does.
Other applications
This is certainly not the limit of INCONEL alloy 625’s uses. Due to the material’s high resistance to potable and salt water, it is often used in pipelines with the purpose of collecting sour gas. The pipelines themselves can either be built using INCONEL alloy 625, or for a more economical alternative, clad in the alloy.
The alloy can be put to use in seawater heat exchangers, power plants and offshore topside services. It is also used for other seawater uses such as mooring cables, propeller blades for boats, propulsion motors, transducer controls and fittings for submarines, and exhaust ducts for utility boats. It also has the potential to be used in components for submerged controls, electrical cable connectors and components for oceanographic instruments.
Out of the sea and in the air, INCONEL alloy 625 plays a large part in the aerospace industry. Thanks to its high tensile, creep and rupture strength, and excellent weldability, it can be used for things like aircraft ducting systems, exhaust systems, thrust-reverser systems and many other technical components. It’s incredibly useful for fuel and hydraulic line tubing, and heat exchanger tubing, where temperatures can rocket.
INCONEL alloy 625 is also used in chemical processing, where both corrosive media and very high temperatures are present within the volatile environment. Its ability to withstand high pressure makes it a material of choice in this delicate arena. It can be welded and fabricated easily into a variety of components, and it can be used with other materials to create thinner-walled vessels that help to save overall weight without sacrificing heat transfer. It can also be used for bubble caps, tubing, reaction vessels, distillation columns, heat exchangers, transfer piping and valves within chemical processing plants.
It also has some nuclear applications, particularly for reactor core and control rod components in nuclear water reactors. In these conditions, integrity of materials is paramount to prevent system failure, so INCONEL alloy’s all-round capabilities come into play. Its ability to resist pitting in high-temperature (260-316°C) water makes it a perfect candidate. It’s also being considered for use in more advanced reactor concepts – proving that the material still has potential applications that haven’t even been devised yet.
INCONEL alloy 625 has been in service and development for decades, moving with the times and providing solutions to even the most modern of problems. Its popularity certainly shows no sign of waning just yet.
Contact us today to find out how INCONEL alloy 625 could be used in your next project, by talking to one of our experienced Sales team.