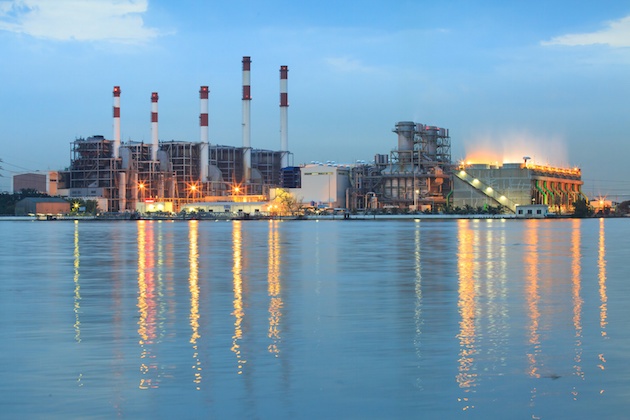
Known for being a world leader in the invention and production of high-quality performance alloys, Special Metals has been operating since 1835. In that time, it has contributed a huge number of alloys to the industry that we all rely on thanks to their use in critical industries.
While some alloys have been around for decades and have stood the test of time to remain in heavy use today, other alloys have been created for a very specific purpose to meet modern needs and requirements. This is particularly true of INCONEL alloy 740H, a custom-engineered alloy designed to meet the growing demands for global energy. In the world of power generation, there is a need to ensure that equipment continually develops to give, reliable, efficient and yet environmentally friendly energy, whether this is in coal-fired, natural gas, nuclear or renewable units.
INCONEL alloy 740H was developed to help meet these tough requirements, helping power generation facilities to cope under the demands of high-pressure and high-temperature environments. It’s specifically designed for its use in Advanced Ultra-Supercritical (A-USC) power generation and made the A-USC Steam Header possible.
Key properties
INCONEL alloy 740H is a nickel-base, precipitation hardenable superalloy with a high content of chromium (24.5%). The alloy is also age-hardened by the precipitation of a second phase, and the hardener content of niobium, aluminium and titanium gives the alloy good thermal stability and high strength.
As A-USC power generation is so important, there are certain considerations that have to be made when selecting the right alloy for the right systems and parts. For example, fireside corrosion can result in metal loss, but A-USC boiler technology requires an alloy that guarantees less than 2mm metal loss in 200,000 hours at an operating steam temperature of 700°C. Steam oxidation resistance is also a key part of the selection procedure, particularly for boiler, superheater and reheater tubing, the header and transfer piping. Steamside oxidation could potentially compromise the structural integrity of the components.
INCONEL alloy 740H’s composition gives it excellent corrosion resistance in high-temperature situations, making it a good choice for these components that are exposed to fireside corrosion on the outside and steamside corrosion on the inside. In tests, INCONEL alloy 740H proves up to the job, which is why it is routinely chosen as an alloy for use in power-generation projects, fulfilling its purpose in creation.
Treatment and working
This superalloy is usually supplied in a solution-annealed and age-hardened condition. It is normally welded in this condition with matching alloy 740H filler metals for use in power boiler service, using both GTA and GMA welding procedures.
The welding method is determined by the parts being created in most cases. For example, for heavy-section header pipe welds, the Hot-Wire Gas Tungsten-Arc Welding (HWGTAW) process is often employed. For the field welding of superheater tubes, however, Gas Tungsten-Arc Welding (GTAW) is more a likely procedure.
INCONEL alloy 740H is certainly a superalloy that has earned its place in the modern world, but it is also testament to the importance of continual innovation in alloys to continue to meet the growing global energy needs.