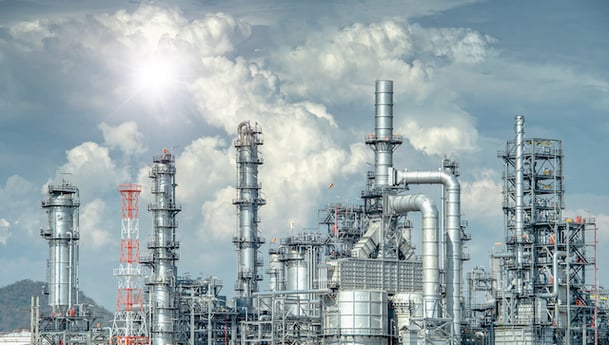
When you’re looking for a good all-rounder, INCONEL alloy 600 is a material worthy of consideration. This high-performance alloy has been a standard engineering material since its introduction in the 1930s.
With excellent resistance to both corrosion and heat, high strength and good workability, this alloy has proven to be a versatile and reliable option. Its uses are not limited to any one industrial sector. INCONEL alloy 600 can be found in everything from chemical applications to aerospace projects, heat-treating machines to electronics.
The perfect composition
A perfect blend of components, INCONEL alloy 600 is a nickel (minimum 72%) and chromium (14-17%) mix. This powerful combination imparts a high level of resistance to many common forms of corrosion. A solid amount of iron (6-10%) in the mix ensures that the alloy is also strong.
With a measured amount of nickel, the resulting alloy is exceptionally resistant to chloride-ion stress-corrosion cracking. Usually, austenitic nickel-chromium stainless steels can fail due to stress-corrosion cracking. This is particularly true in environments where there is chloride present, as well as other compromising factors. However, because the amount of nickel is controlled in INCONEL alloy 600, it is considered virtually immune to these unwanted and potentially catastrophic effects.
Meanwhile, the chromium content is responsible for its resistance to oxidising conditions, caused by high-temperature or corrosive environments. With a potential service operating temperature from cryogenic to above 2,000°F (1,095°C), it’s clear why this material is so valued.
The alloy can only be hardened and strengthened by cold working. In its annealed condition, it has a yield strength of 25,000 to 50,000 psi. Following heavy cold working, the material can even reach a tensile strength of 220,000 psi.
Key specifications
One of the most notable attributes of INCONEL alloy 600 is its corrosion resistance. Its specific composition gives it quite a wide range of resistance under many conditions. The chromium balance ensures that it’s superior to commercially pure nickel in oxidising environments. The nickel gives the alloy its natural resistance to reducing conditions and alkaline solutions.
The alloy is also selected for its ability to withstand high-temperature environments. In tests, it’s shown to have good resistance to carburisation in high temperatures, as well as oxidation and scaling. It can also resist attack by sulphuric compounds, to a degree.
The material is highly workable, readily fabricated by either hot or cold working. It can be easily joined using standard welding procedures. It can also be heat treated for maximum strength, depending on the end use of the material. Usually, it’s treated in such a way as to give it a fine grain structure, which is often preferred because it gives better corrosion resistance and higher tensile, fatigue and impact strength.
General uses and applications
When it comes to applications, this is a particularly versatile material. It’s found across a number of different industries as a base material of construction.
In chemical processing, for example, it’s often used in the manufacture of heaters, stills, bubble towers and condensers. It’s also used in the pulp and paper industry where equipment comes into contact with abietic acid. This acid is an organic compound found in trees that is considered non-hazardous. However, through oxidisation it can become more corrosive. INCONEL alloy 600, with its high corrosion resistance, is therefore a useful option for processing plant components.
Due to its ability to withstand high temperatures, it’s no surprise that INCONEL alloy 600 is also used in the heat-treating industry. It can be found in, among other things, retorts, muffles, roller hearths and furnace components.
INCONEL alloy 600 is used in the aerospace industry, particularly in the construction of jet engines. These high-pressure and hot components are demanding. The alloy is used for things like exhaust lines, turbine seals, lockwire, and other engine and airframe components.
You will also find INCONEL alloy 600 in use within the electronics field. Here its applications include things like cathode-ray tube spiders, thyratron grids, tube support members and springs.
Nuclear applications
Nuclear power can be a somewhat controversial topic. Its presence in the media often swings between the positive and the negative. The Hunterston B nuclear power station in Scotland is being decommissioned from 2022, after cracks were found in its nuclear core. It has contributed to the UK energy sector for over 40 years. But as some nuclear sites close, it’s still an industry that’s moving forwards. A Bill Gates founded nuclear energy venture is looking at building small advanced nuclear power stations that can store electricity. The idea is that they can supplement grids supplied by solar and wind power when needed.
If there’s any industry that needs absolute reliability and performance from its construction materials, it’s the nuclear field. If the materials used are compromised, the results can be catastrophic. Yet the conditions that these materials are used in are tough. As well as high temperatures, the water systems of the reactors contain high-purity water. This water can attack materials and cause intergranular stress-corrosion cracking (SCC).
INCONEL alloy 600, as we’ve mentioned, exhibits excellent resistance to SCC; it’s virtually immune under normal conditions. As such, it’s a standard material of construction in the nuclear industry for basic components in the water systems. In order to maintain this exceptional resistance to SCC in these challenging conditions, INCONEL alloy 600 is made to even more exacting specifications than usual. This has its own designation, INCONEL alloy 600T.
Contact us today to find out more about INCONEL alloy 600 and how it can be used in your next project.