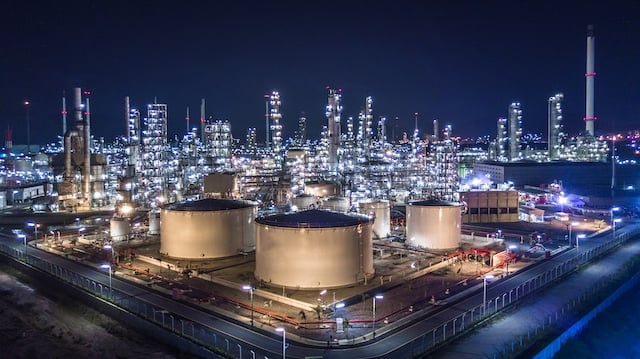
The processing of volatile substances is an essential industrial undertaking, however it comes with many problems. Not least the selection of suitable materials used in the manufacture of equipment that forms part of the processing machinery.
In chemical processing, equipment needs to be able to withstand the highly corrosive contents it will be exposed to without losing structural integrity. This is why nickel-based alloys are so popular within the chemical processing arena – they are designed to withstand all kinds of chemical corrosion. They are also built for strength, even under pressure and high temperatures, resisting metal fatigue in the most extreme of environments.
Hydrocarbon processing is one of the most important industrial functions – it is our primary energy source after all. Large-scale oil refineries process hydrocarbons for use, while crude oil can be refined to form the necessary hydrocarbons. Without effective systems for processing, we can’t meet the necessary global demand.
The team at Corrotherm has vast experience of working within the chemical and hydrocarbon processing sectors. Our knowledge means that we can advise our customers on the best nickel alloys to suit their needs. When it comes to this difficult industry, the MONEL range of products offers many benefits.
Why MONEL?
The MONEL range of alloys are created with nickel and copper, making them strong, corrosion resistant and cost effective. By adding in carefully controlled amounts of other alloying elements, these materials have desirable specifications for a range of industrial applications.
MONEL alloy 400 is widely used in hydrocarbon processing. It is employed in the construction of petroleum distillation towers for internal components and parts, including valves, pumps, fasteners and fittings. Having been on the market for over 100 years, this alloy still remains a popular choice for modern process vessels and crude petroleum stills.
Its composition is 63% nickel as a minimum and 28-34% copper. Its characteristics are similar to commercially pure nickel, but its lower cost makes it more practical for use in large-scale operations.
MONEL alloy 400 has been developed and evolved over the years to meet the increasingly difficult criteria required of materials in the modern processing industry. By adding very carefully controlled quantities of titanium and aluminium to the basic mix, we get MONEL alloy K-500.
This is a precipitation-strengthened version of the base alloy, which can be hot or cold worked and heat treated, to give an extremely powerful material. It is both stronger and tougher than the base MONEL alloy 400.
As such, MONEL alloy K-500 is often selected for use in oil extraction and chemical processing, where its exceptional corrosion resistance coupled with high strength solves many engineering problems.
In some processing equipment, both MONEL alloy 400 and MONEL alloy K-500 are used in combination, to give the perfect blend of both alloys.
If you want to find out more about the use of MONEL alloys in chemical and hydrocarbon processing, please give our friendly and knowledgeable team a call. Contact us today.