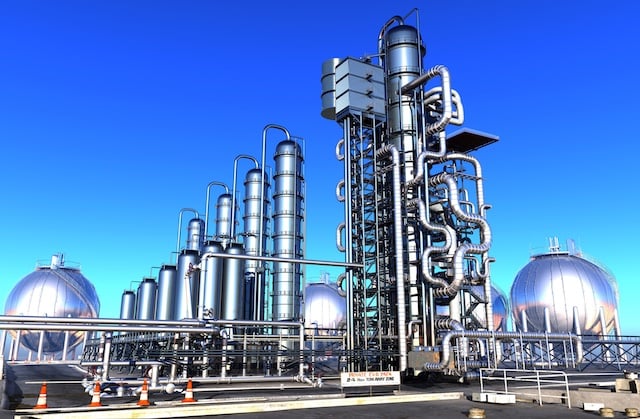
Many alloys are prone to corrosion under certain conditions, particularly in the case of iron or steel which can rust in the presence of oxygen. By applying a coating, usually pure zinc, the corrosive elements can’t reach the base metal and hence the corrosion does not occur.
History of galvanization
This process is known as ‘galvanization’, a term that derives from the name of an Italian scientist called Luigi Galvani. Galvani had many important discoveries, most notably in the field of bio-electromagnetics. Since his death in 1798, his name has survived in the form of a verb, ‘to galvanize’. One of the meanings of this is ‘to stimulate or excite as if by electric shock’ or ‘to subject to the action of an electric current especially for the purpose of stimulating physiologically’, which is directly related to Galvani’s work in animal electricity. It is often used metaphorically too – ie to galvanize a group of people into action. Its other key meaning is ‘to coat with zinc’.
It is this latter definition that is relevant to metallurgy. Galvanization has a long history, before the term was properly applied to it. There are examples of galvanized iron armour from the 17th century. While the galvanization process almost exclusively refers to the use of zinc to reinforce metals, other metals and alloys have been utilised throughout the years.
Methods of galvanization
The most common form of galvanization in industry is called ‘hot-dip galvanizing’. You can also get galvanic paint for small-scale and personal use. This is painted on to steel or iron surfaces to lend them a corrosion-resistant property, ie to give a surface rust protection. In the automotive industry, electro-galvanizing is often used, which offers a thinner layer of the coating and a better aesthetic appeal.
Hot-dip galvanizing involves dipping a metal into a hot bath of molten zinc, which is usually heated to around 449°C. The metal is thoroughly cleaned with a caustic solution before dipping to ensure there are no deposits that could prevent the coating from bonding. It is then rinsed and run through an acidic solution to gets rid of any scale, which again could stop a good bond. A flux (cleaning agent) of zinc ammonium chloride is applied before the metal is dipped into the molten zinc bath.
After the metal is removed from the hot bath, fully coated, it is quickly cooled and the zinc begins to react with the oxygen in the atmosphere, which forms zinc oxide. This then reacts with the carbon dioxide, which produces zinc carbonate, the final layer that provides protection to the base metal from outside elements. It’s a process that often leaves a tell-tale crystallised pattern on the surface.
Zinc-nickel coatings
The most common coating used in galvanization is pure zinc, though there are some circumstances when a zinc-nickel coating could be used instead. It has been used with success across the aerospace and automotive industries, for example. Normally this is used in electro-galvanizing, or electroplating, rather than hot-dip galvanizing.
The standard ratio is in the region of 85% zinc and 15% nickel, and is electroplated on to steel or iron in the same way as the traditional pure zinc coating. However, it has been shown to offer greater corrosion resistance and more protection against wear on moving components. It also creates a smooth, hard base that is well suited to painting, which is why vehicular uses are the most widely recognised examples of zinc-nickel alloy coatings.
Galvanization is an important industrial process that adds longevity and protection to common components and structures.