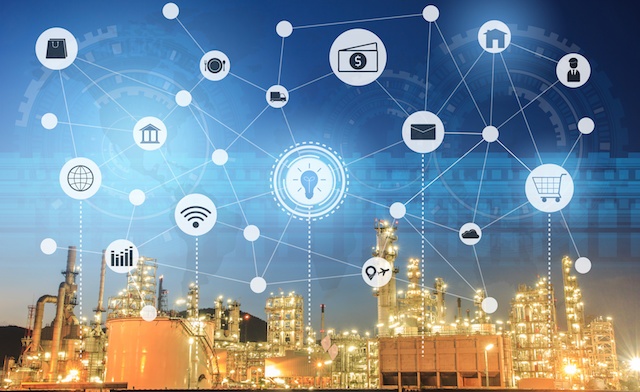
‘Digital manufacturing’ sounds like a bit of an oxymoron. Manufacturing is traditionally a manual trade, with physical products being produced and assembled in factories around the world. However, the digital revolution that has engulfed almost every industry is making its way into the world of manufacturing. Companies have the opportunity to embrace it now and pave the way for a bright future.
We’ve already seen advances in certain areas of manufacturing, such as additive manufacturing (3D printing) and robotics. Automation and a switch to a servitisation model are becoming real possibilities for some businesses. The role of technology in today’s manufacturing industry is significant.
Digital innovation will inevitably change the future of manufacturing, from the ways in which we research and development new products, to the way we deliver them to our customers.
Data is the driver
Behind the advancements of digital manufacturing is a lot of data. We have the ability to collect better data and information than ever before. Many companies have access to more data than they know what to do with, and a lot of it is wasted.
Being able to harness this data and use it effectively can change the way that a business operates. For example, digital asset management can be used to monitor vast amounts of data related to a component in a machine. The data is analysed so that the component can be repaired or replaced as soon as it is needed, rather than reporting a fault, waiting for an engineer and ordering a new part.
This will develop even further so that a component will be digitally tracked throughout its entire product cycle, always being exactly where it needs to be automatically. This will save both time and money for businesses.
Data analysis can also monitor a manufacturing factory’s processes and identify areas for improvement in a way that has never been possible before. Advanced computing algorithms can find time-saving tricks that can speed up production time and reduce wastage.
The benefits of going digital
While some manufacturing businesses may be initially reluctant to adopt these new processes and technologies – if something isn’t broken, why try and fix it? – there are plenty of clear potential benefits.
Automation systems help factories to work more efficiently. By removing tasks like stock ordering, which can be entirely automated, employees can be retasked into other areas, improving productivity. It also means that the response time for performance issues can be vastly improved, which ensures less downtime and better customer delivery.
With every part of a production chain linked digitally, it also means there can be better communication between different roles. A supplier, a designer, an engineer, a production company, a sales team… everyone can access the same data and share knowledge. This helps with quality control, maintaining standards, dealing with problems and striving for improvement.
We’re excited about the future of digital manufacturing and the changes this will bring in the UK and beyond.