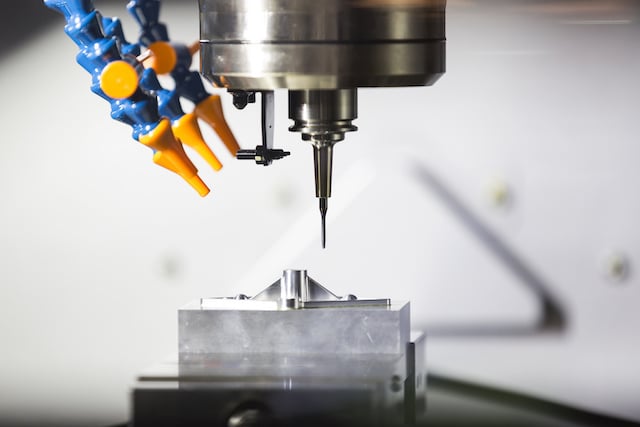
Many industries are seeing the benefits of additive manufacturing, particularly those where bespoke parts can be expensive to design and produce to exact specifications. One of the early adopters of the 3D printing process was the aerospace industry, which recognised its potential from the outset. It also contributes to the ongoing development and innovation in the additive manufacturing area.
There are clear advantages to implementing 3D printing methods in the manufacture of parts for aerospace use. For a start, the components are incredibly detailed and complex, requiring a skill in micro-precision engineering to work with the extremely tight and minute tolerances. Computer-generated designs coupled with 3D printing methods help create these detailed parts much quicker and with less material waste. Not only that, 3D printers open up the opportunity to create parts that would be impossible or incredibly difficult to make using traditional methods.
In turn, this helps to push forward innovation in the industry, the limitations of traditional manufacturing removed from the equation. This then opens up more opportunities for design engineers to broaden the scope of their creations, producing aerospace designs that are more economical to fly and more sustainable too.
The sustainability factor
Sustainability is another key area that is important for aerospace. Parts inevitably wear down over time and repairs can be time-consuming and costly. Grounding an aircraft for repair and maintenance work means lost income. However, when parts can be created as and when they are needed, to exact specifications, there is no waiting around for a part to make its way through the production chain. Combined with smart monitoring systems, which anticipate repair work in advance and the ability to prepare by ensuring the right materials are ready, maintenance time is decreased, leading to productivity gains.
There are less tooling changes required, another way that 3D printing components helps to increase productivity, and turnaround times are quicker. The process produces little to no waste, helping businesses meet their environmental targets. Parts can also be created that are lighter, which leads to reduced fuel consumption, saving precious resources.
The future
Clearly, additive manufacturing is already starting to have a measurable impact on the aerospace industry. It is opening up potential innovation and creating a more sustainable environment. But this is just the start – 3D printing is set to have an even greater place in aerospace over the next decade.
For now, the focus is on creating small-scale parts for existing aircraft. Which in itself has created the biggest revolution in the industry in recent years. But the future offers even more potential. There is scope for entire 3D-printed frames, which could lead to fast, light and efficient planes.
There is some development in this area already, although not quite on the scale of a commercial aircraft. For example, the team at Soleon have used 3D printing to improve its agricultural drone. With a new laser-sintered polyamide body, this pest-control unmanned aerial vehicle is lighter and faster, as well as a prime example of the potential of the manufacturing process.