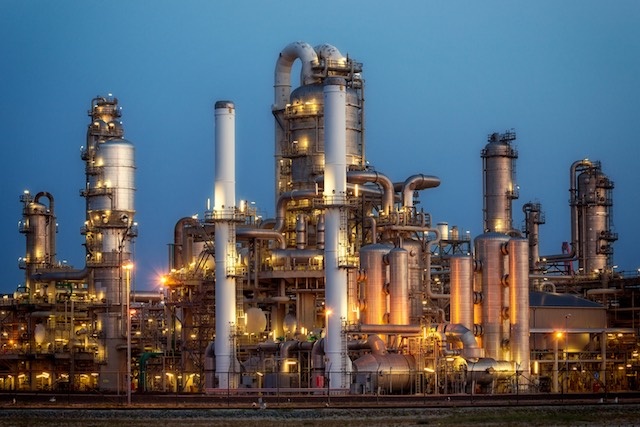
Both INCONEL and INCOLOY alloys are based on nickel and chromium, with significant other additions. The two elements work together and are a popular base for superalloys. They are famed for their exceptional corrosion resistance, as well as their high-temperature performance. However, there are other characteristics that make nickel-chromium-based superalloys so technically superior.
The term ‘superalloy’ itself refers to a very specific breed of materials. It’s an alloy that can withstand high temperatures, high stresses and highly oxidising atmospheres. Nickel-chromium based alloys fit into this group. These alloys must be manufactured by experienced professionals, as the metal is hard to shape and machine using traditional techniques. This is why Corrotherm only works with trusted suppliers, to assure quality.
The role of chromium
The composition of these superalloys has to be exact to give the desired properties. Chromium is soluble in nickel, creating a solid solution on which the alloys are based. The right amount of chromium needs to be added, as small amounts (of less than 7%) increase the sensitivity of a nickel-chromium alloy to oxidation. Adding more than 7% and up to about 30%, and the situation is reversed, giving the alloy resistance to oxidising media.
We’ve previously looked in detail at the properties of chromium and how its addition to superalloys imparts both strength and corrosion resistance. For the most outstanding of technically superior alloys, it makes up approximately 20% of the composition.
For example, in the ever-popular INCONEL alloy 625, the chromium content of 20-23% is part of the reason why this nickel alloy is so exceptionally strong and super resistant. The combination of elements in this material give it superior resistance to corrosive environments of unusual severity.
High-temperature performance
Superalloys created from a base of nickel and chromium are the material of choice when it comes to working in high temperatures. This is because when temperatures top 540°C, common steel and titanium alloys become more vulnerable to corrosion attack. With the right blend of elements, a superalloy can show strength at 1000°C that exceeds that of an ordinary steel at room temperature. While some refractory metals have higher melting points than nickel-based alloys, they don’t retain the same strength properties in extreme environments.
It is not just the nickel and the chromium that give a superalloy this impressive characteristic. Other compositing elements include molybdenum, which is notable for its excellent strength and mechanical stability. It remains tough and ductile at very high operating temperatures. Molybdenum-containing superalloys are often employed for things like gas turbines in both the aerospace industry and on land. For example, INCONEL alloy 718 has molybdenum added and this material can be used for components in turbines, liquid-fuelled rockets, rings, casings and cryogenic tankage.
Find out more about superalloys on the Grades page or Contact a member of the team to discuss your nickel alloys requirements.